Customized tests
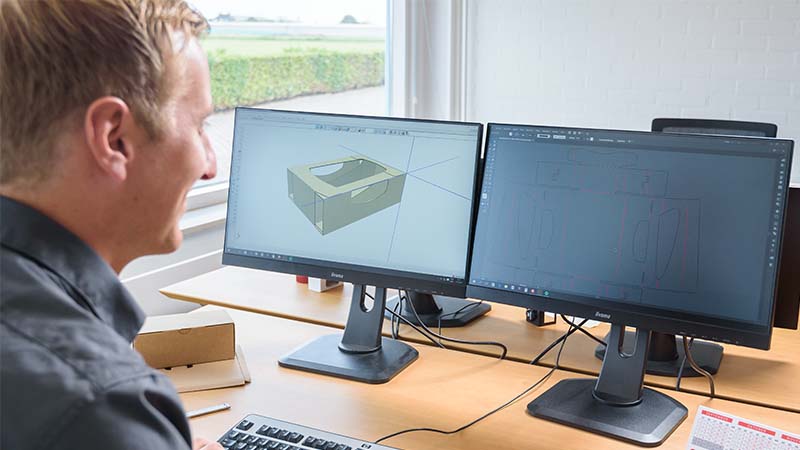
For unique products, special ways of transport, or for new wishes, an international test standard is not always available. No problem, because this the sort of challenge a packaging engineer loves.
Together with the client, a creative solution is developed. And, if necessary, developed, built, and performed. This has often led to surprising and interesting tests.
Rain test
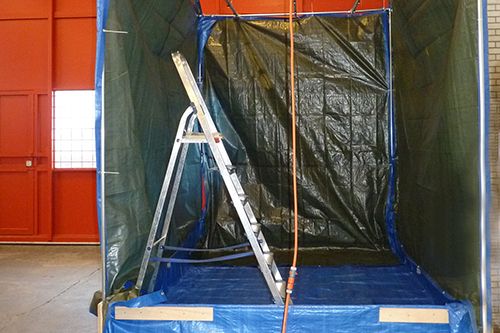
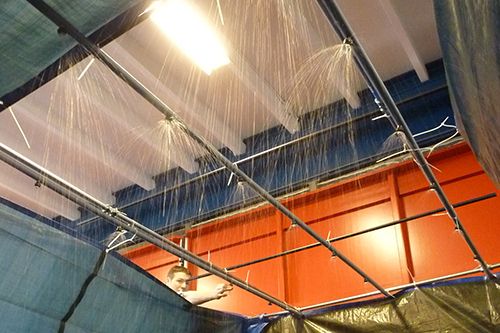
A supplier of insulating materials wanted – because of alternating production peaks and resulting storage capacity – to be able to temporarily store materials outside. In the Netherlands, this does require the insurance that this is sufficiently protected against rain.
Therefore, Topa Institute has developed the ‘Rain Test’, exclusively for this purpose. By creating a setup of sprinklers from the agricultural sector, the protective film could be tested for rain. The protection was tested, and it was also investigated what the minimum amount should be. By means of ASTM standards, the amount of water was determined, among other things
Shopping bag test
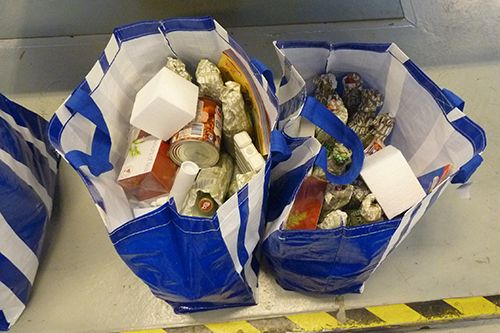
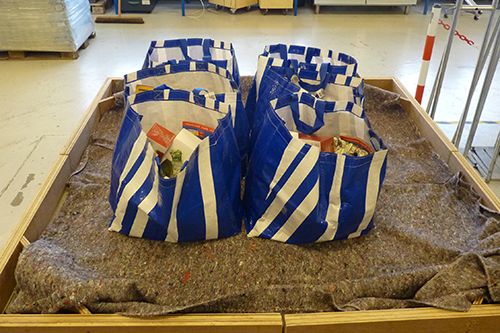
In most tests, the transport for complete pallet loads or general cargo is simulated. But during the ‘Last Mile’, the product has to undergo certain things, too. The ‘Last Mile’ is the last transport a packaging undergoes: usually by the consumers from the store to their homes. For instance, there is the example of individual beer bottles that can be put in a shopping bag in between all sorts of other products. Everyone understands that glass can break, but if the labels are damaged quickly or become unreadable due to friction with other objects, this is unacceptable to both the producer and the consumer.
By mimicking the transport exactly, the various labels were tested and it became clear which label could withstand these conditions. The test equipment of Topa Instituut was adjusted to let a shopping bag with various products as well as the beer bottles vibrate, shake, and move.
Tip-over-test
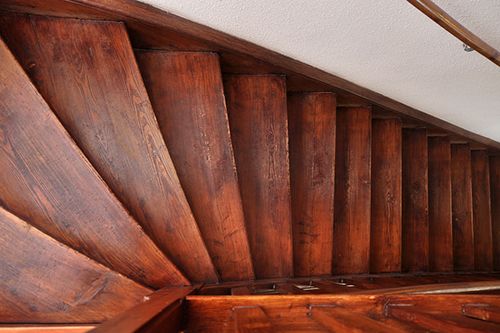
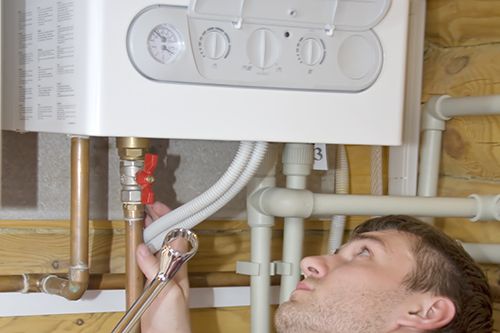
Topa Instituut has developed the ‘Tip-over-test’ for a supplier of boilers. The transport of a boiler usually always occurs upright. All international test standards have been developed accordingly. However, the supplier still suffered damage. Therefore, Topa Instituut reviewed the actual transport. After all, this is step 1 of the 5 step plan.
This showed that 99% of the transport occurred vertically. However, in the last moment – the moment that the boiler was placed in the attic – the boiler had to be placed in the attic horizontally first in some cases. And this appeared to be the problem.
After this discovery, a test was developed. The producer made a small adjustment to the construction and subsequently, it was investigated how the boiler could best be protected during this last part of transport by means of a test.